An integral part of any airport’s infrastructure, the construction of a runway is a significant investment. The intricate planning and construction of a runway can easily take several years, depending on various factors. But how much does it actually cost to construct a runway?
The figures discussed in this article are based on constructing runways at major commercial airports, where runway lengths and widths are typically 30-45 meters wide and +1500 meters long. These metrics are typical of the majority of commercial airports around the world.
How Much Does It Cost To Build An Airport Runway?
While a specific construction cost cannot be given as each runway project will differ due to infinite variables (runway size, labor costs, material costs, etc), it is not uncommon for runway construction costs to amount to hundreds of millions of dollars.
There are also some outliers to this bracket, as several US-based runway construction projects have amounted to over 1.1 Billion US dollars – the most noticeable being at Chicago O’Hare International Airport and Atlanta Hartsfield Jackson Airport.
When these figures are presented, it is important to consider the cost breakdown associated with the total construction amount. The costs can be broken down into several key areas:
- Planning
- Construction
- Testing
Planning
In the planning phase of a new runway, specifications need to be established for the new infrastructure. This involves determining what the new runway will be used for – the types of aircraft and their respective Maximum Takeoff Weight (MTOW) being a key indicator.
When the length and width of the runway are determined, a detailed series of geophysical surveys will take place at the construction site. These surveys will gather data regarding the land and environment in which the new runway will be located. The prevailing weather conditions/winds, and potential obstacles in the vicinity of the runway are identified.
Depending on what weight class of aircraft will be operating on the runway, the ground below the runway will have to be inspected to ensure the necessary structural reinforcements can be implemented.
A structural engineering team will perform stress tests to ensure that sufficient underground support is in the design.
Aside from structural tests, a drainage system will have to be designed to provide adequate removal flows for water across the runway surfaces.
The costs associated with planning and designing a runway can amount to $10 million – due to the need for industry-specific consultancy services.
Concrete vs Asphalt Runway
With over 80% of major commercial airports being constructed of asphalt runways, they are the most common material found on runways. This is mainly due to the lower construction costs when compared to concrete installation.
While asphalt runways are cheaper to construct, they are less durable than concrete – which leads to cracking and general wear/tear over time. This requires ongoing, regular maintenance that can be costly over a prolonged period of time (several decades).
However, with the correct maintenance, asphalt runways can have a 30-year lifespan before major refurbishments or resurfacing requirements.
Concrete runways also have a longer installation time when compared to asphalt runways – which generally take 30-40% more man-hours to construct.
Costs to Build a Concrete and Asphalt Runway
For a direct price comparison, in the United States, you can expect to pay $2-$4 dollars per square foot for asphalt versus $5-$7 dollars per square cost for a concrete installation. With an almost double construction cost, it is clear as to why asphalt is the preferred material for constructing large, commercial runways.
Construction
When plans for a new runway are finalized, construction contracts are tendered. The expertise and labor hours required to complete a runway can amount to up to 12 hours a day, which can last for several years until the completion of the runway.
With the requirement for a high degree of expertise and experience in runway construction, qualified contractors and consultants can be expensive to hire – often involving contracts worth tens of millions of dollars.
While these contracts can be agreed on a fixed amount, it is not uncommon for additional costs to be incurred due to project delays etc.
Testing
Upon completion of a new runway, the airport operator will generally have phases for commissioning the runway into service. The initial phases will involve a staggered, limited operating window for the new runway, in which traffic flows will be sent to the runway.
While this process does not directly have any expenses, there can be revenue lost in terms of utilization – in instances in which problems are identified. While these problems are troubleshooted, there can be operational disruptions.
Average Cost to Build a Runway
As mentioned above, there is no specific or set cost for constructing a new runway. However, a realistic ballpark average cost would be $150-300 million for a 2,500-meter asphalt runway.
Conclusion
In conclusion, the construction of a runway at a major commercial airport is a significant investment that can cost hundreds of millions of dollars. The actual cost varies depending on several factors, including the size of the runway, labor costs, material costs, and location. Runway construction projects at some US airports have exceeded $1.1 billion.
After completion, the runway undergoes testing and commissioning phases, which may result in operational disruptions and potential revenue loss during troubleshooting.
Overall, the construction of a runway is a complex and costly endeavor that requires careful planning, skilled labor, and ongoing maintenance to ensure the safe and efficient operation of an airport.
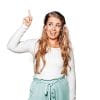
After visiting more than 60 countries, I have probably been on every type of plane there is and visited countless airports. I did my very first international solo trip to South Africa at the age of only 16 and haven’t really stopped traveling since.
Despite the adventurous travel itch, I do have a nerdy side as well – which is satisfied by writing about all things aviation “too boring” for my regular travel blog.